ΤΡΟΧΟΙ PART IΙ
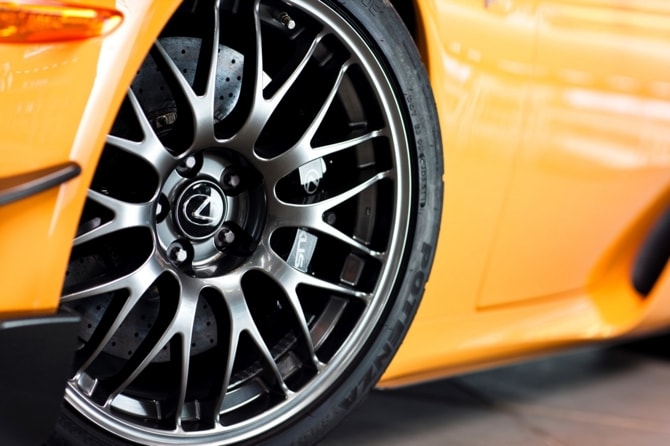
Ζάντα ή ..λεζάντα?
Πήρατε την πρώτη γεύση τον προηγούμενο μήνα, στο Part I, συζητώντας γενικώς περί τροχών του αυτοκινήτου και για τον πολυδιάστατο ρόλο που αυτοί παίζουν ως σύνολο στη συμπεριφορά και τις επιδόσεις του οχήματος, τόσο ποιοτικά, όσο και ποσοτικά, βάσει της μάζας τους. Καιρός να «σπάσουμε» τώρα τον τροχό στα δύο βασικά μέρη που τον απαρτίζουν, την ζάντα και το ελαστικό, και να τα ξεφτιλίσουμε στην ανάλυση όπως μόνο εμείς στο POWER ξέρουμε. Θα ξεκινήσουμε εδώ από τον πιο «σκληρό» της υπόθεσης, την ζάντα.
Είναι απίστευτο το εύρος των διαφορετικών τύπων ζαντών που συναντά κανείς πλέον σήμερα στην αγορά και όταν λέμε «τύπων», στο καλάθι των επιλογών μας πραγματικά μπαίνουν αμέτρητοι παράγοντες που πρέπει να λάβουμε υπόψη: για δεδομένο χρηματικό μπάτζετ και αφού καταλήξουμε στη διάσταση που πρέπει (και όχι πάντα που θέλουμε..!) και φιλτράρουμε και τα σχέδια που γουστάρουμε, η κάθε υποψήφια ζάντα μπροστά μας είναι σίγουρο ότι θα έχει διαφορετικά χαρακτηριστικά από την διπλανή της, ακόμα κι αν αυτά δεν φαίνονται κατευθείαν «με το μάτι». Για την κατασκευή μίας «καλής» επώνυμης ζάντας, όπως θα δούμε αναλυτικά παρακάτω, τα εργοστάσια που ασχολούνται με το άθλημα πραγματικά «ξεζουμίσουν» ολόκληρη τη φαρέτρα των όπλων που τους προσφέρει η σύγχρονη τεχνολογία κατεργασίας των υλικών. Μπορεί σαν τελικό προϊόν μία ζάντα να φαίνεται μηχανουργικά «απλό», χωρίς πολλά φρου-φρου και αρώματα, ωστόσο τα βήματα που θα περάσει η πρώτη ύλη μέχρι να φτάσει τελικά στο ράφι του ζαντολαστιχά σας είναι πάμπολλα και ενδιαφέροντα. Το ακριβές “know-how” κάθε κατασκευαστή ζαντών είναι και αυτό που εν τέλει αντικατοπτρίζεται στην τιμή που καλείστε να πληρώσετε στο ταμείο του προαναφερθέντος ζαντολαστιχά: δεν είναι τυχαίο που θα βρείτε π.χ. μία 17x7 με χ ευρώ και κάποια άλλη, όχι αναγκαστικά ελαφρύτερη αλλά σίγουρα ποιοτικότερη, με διπλάσια ή και τριπλάσια τιμή. Σήμερα και οι δύο μπορεί να σας φαίνονται απαστράπτουσες και όμορφες, ωστόσο μετά από πενήντα καλές λακούβες, τριάντα σκανταλιάρικα πεζοδρόμια, κάνα-δύο χρόνια επιβίωσης σε υγρό και αλμυρό κλίμα ελληνικού νησιού, πέντε ζυγοσταθμίσεις ή εκατό γύρους στη πίστα, η φτηνή μπορεί να είναι ερείπιο για πέταμα, ενώ η ακριβή του κουτιού με ένα πολύ απλό εξειδικευμένο ανασκούμπωμα. Μπορεί πολλοί λοιπόν να αγοράζουν ζάντα για τη λεζάντα, αλλά εσείς δεν είστε από αυτούς, εσείς διαβάζετε POWER, φύγαμε!
Σιδερένιες: παλιοσίδερα…ή μήπως όχι?
Η τυπική ζάντα («σώτρο» ελληνιστί) αποτελείται από δύο βασικά μέρη: το δίσκο (το κεντρικό κομμάτι το οποίο πιάνει στο μουαγιέ μέσω των οπών για τα μπουλόνια ή το μπουλόνι) και τη στεφάνη, η οποία «τυλίγεται» περιφερειακά του δίσκου. Ανάλογα με τη μέθοδο κατασκευής, όπως θα δούμε, ο δίσκος και η στεφάνη μπορούν, είτε να διαμορφώνονται μαζί από κοινού κατά την εκάστοτε κατεργασία (χύτευση ή σφυρηλάτηση «μονομπλόκ»), είτε να κατασκευάζονται ξεχωριστά και να παντρεύονται στη συνέχεια μεταξύ τους μέσω κατεργασίας συγκόλλησης. Η πιο απλή και φτηνή κατηγορία ζαντών είναι οι παραδοσιακές «σιδερένιες», οι ζάντες δηλαδή με τις οποίες συνήθως εξοπλίζει το εργοστάσιο τα αυτοκίνητα (ουσιαστικά των μικρότερων μόνο πλέον κατηγοριών) στις «βασικές» τους εκδόσεις. Στην πραγματικότητα θα έπρεπε να μιλάμε για «ατσάλινες» ζάντες, αφού ποτέ δεν χρησιμοποιείται ατόφιο «σίδερο», αλλά πάντοτε σε κράμα με άνθρακα. Οι ατσάλινες ζάντες κατασκευάζονται είτε με χύτευση, είτε, ακόμα συχνότερα, σαν πρεσαριστές με τα αντίστοιχα καλούπια. Στη δεύτερη περίπτωση η διαδικασία έχει ως εξής: η στεφάνη ξεκινάει τη ζωή της ως ένα απλό παραλληλόγραμμο φύλο χάλυβα το οποίο, αφού καμφθεί για να έρθουν οι άκρες του να συγκολληθούν μεταξύ τους και να σχηματιστεί ο κύλινδρος, στη συνέχεια αυτός περνάει από διαφορές «περιστροφικές» κατεργασίες της ευρύτερης κατηγορίας των τόρνων ώστε να δημιουργηθεί το επιθυμητό πάχος προφίλ κατά πλάτος του (οι «ώμοι» και τα «χείλη» που θα έρθει να πατήσει το λάστιχο στη συνέχεια). Ο κεντρικός δίσκος της ζάντας, αφού περάσει από τη πρέσα και τις υπόλοιπες διαδικασίες διάνοιξης π.χ. των οπών εξαερισμού, μπουλονιών ή βαλβίδας, ακολούθως περιφερειακά συγκολλείται στην εξωτερική πλευρά της έτοιμης στεφάνης. Ακολουθούν διάφορες βασικές κατεργασίες θερμικές ή βαφής για το τελικό φινίρισμα, ωστόσο σήμερα τις πλέον «hi-tech» κατεργασίες που θα δούμε παρακάτω τις έχουν κρατήσει οι κατασκευαστές ζαντών για τα πιο μοντέρνα κράματα. Συχνά σνομπάρουμε τις ατσάλινες ζάντες γιατί παράγονται σε σχετικά περιορισμένα παλιομοδίτικα σχέδια και επειδή «δεν είναι αλουμινίου», η πλάκα είναι όμως πως συχνά η πραγματική ουσία (κέρδη σε μάζα π.χ.) απέχει παρασάγγας από τη εδραιωμένη αυτή άποψη. Για δεδομένη διάσταση, δεν είναι επ’ ουδενί δεδομένο πως μία ζάντα «ελαφρού» κράματος, και δη από τις «οικονομικές», θα είναι ελαφρύτερη από την αντίστοιχη ατσάλινη! Δεν πρέπει να ξεχνάμε πως μπορεί π.χ. το αλουμίνιο να έχει μικρότερη πυκνότητα από το ατσάλι, αλλά επίσης έχει και χειρότερες επιδόσεις ως προς την αντοχή εφελκυσμού: με άλλα λόγια, για δεδομένο όγκο μετάλλου, το αλουμίνιο θα έχει μικρότερη μάζα, αλλά θα έχει και μικρότερη αντοχή, γεγονός που τελικά επιτρέπει υπό συνθήκες σε μία ατσάλινη ζάντα ίδιας αντοχής να χρησιμοποιηθεί λιγότερο υλικό και να επιτευχθεί μικρότερη συνολική μάζα. Όταν λέμε «υπό συνθήκες» εννοούμε ότι με την βοήθεια της σύγχρονης τεχνολογίας και των υπολογιστικών μεθόδων σχεδιασμού, είτε έχουμε να συγκρίνουμε το ατσάλι π.χ. με το αλουμίνιο, είτε διαφορετικές ζάντες αλουμινίου μεταξύ τους, ο «έξυπνος» σχεδιασμός επιτρέπει να χρησιμοποιήσουμε «λιγότερο υλικό εκεί που μπορούμε» χωρίς να χάσουμε σε αντοχή. Περισσότερα για τον αποδοτικό αυτό σχεδιασμό παρακάτω, αλλά για την ώρα κρατήστε πως μία ατσάλινη ζάντα δεν είναι από τα αποδυτήρια καταδικασμένη να είναι βαρύτερη: κλασικό παράδειγμα είναι οι (made by Michelin) σιδερένιες ζάντες των Rallye, οι οποίες (όπως ανακάλυψαν κάποιοι ψαγμένοι στη ζυγαριά) ήταν ελαφρύτερες από πάμπολλες aftermarket αλουμινίου ακόμα και ίδιας διάστασης. Οι υπόλοιποι «άτυχοι», μεταξύ των οποίων και ο γράφων που έχει το θράσος τώρα να σας το παίζει μάγκας, έδωσαν τα λεφτουδάκια τους για, ουσιαστικά «χειρότερες» από τις εργοστασιακές ατσάλινες, ζάντες αλουμινίου. Η «λεζάντα» που λέγαμε σε όλο της μεγαλείο...
Μιλώντας για λεζάντα, ας κάνουμε και μία μικρή αναφορά (και πολύ τους είναι) στην πιο χαρακτηριστική «βιτρίνα» που χρησιμοποιείται για να γίνουν οι ατσάλινες ζάντες λίιιγο πιο ελκυστικές στο μάτι: το γνωστό μας τάσι. Η συντριπτική πλειοψηφία των τασιών, για μην γελιόμαστε, δεν έχει πρακτική ουσία, κάθε άλλο: χειροτερεύουν την ψύξη των φρένων, ενίοτε τσακίζουν τη ζυγοστάθμιση, φεύγουν από τα ελάσματα τους αν καμφθεί ο τροχός σε «γονατισμένες» στροφές και, πάνω από όλα, δεν βλέπονται. Κυκλοφορούν βέβαια στην αγορά και κάποια ψαγμένα τάσια για ειδικές χρήσεις (θα τα δείτε π.χ. σε διάφορα πρωτότυπα ή οχήματα μαραθώνιων ελάχιστης κατανάλωσης). Αυτά έχουν ειδικά μελετημένη σχεδίαση που φτάνει σε σημείο μέχρι και να μειώνει το συντελεστή οπισθέλκουσας (Cd) του τροχού ή να βελτιώνει την ψύξη των φρένων μέσω της ροής του αέρα που παρέχεται κατά την περιστροφή του τροχού. Αρνούμαι να μιλήσω άλλο για τάσια.
Αλουμινένιες: more than meets the eye
Όπως είπαμε και παραπάνω οι ζάντες κραμάτων αλουμινίου δεν αποτελούν πάντοτε «σιγουράκι» στην μείωση της μάζας των τροχών μας, αλλά αυτό δεν αναιρεί το γεγονός ότι μία καλή και ψαγμένη ζάντα αλουμινίου μπορεί όντως, κατά περίπτωση, να επιφέρει μία σημαντική μείωση στο μη αναρτώμενο βάρος: μείωση του εν λόγω βάρους της τάξεως του 20-25% σε σχέση με την αντίστοιχη ατσάλινη ζάντα είναι ένα τυπικό κέρδος που μπορεί να επιτευχθεί. Υπεύθυνος παράγοντας για το προαναφερθέν κέρδος στο βάρος, όπως υπονοήσαμε νωρίτερα, δεν είναι τόσο από μόνο του το γεγονός πως «εκ φύσεως» το αλουμίνιο είναι καθαυτό ελαφρύτερο σε πυκνότητα από το σίδερο, όσο η εφαρμογή σύγχρονων μεθόδων κατεργασιών κατά την κατασκευή. Η εξέλιξη των κατεργασιών αυτών, από κάποιο χρονικό σημείο και μετά επέτρεψε στους κατασκευαστές ζαντών να εκμεταλλευτούν πλήρως τις ιδιότητες των κραμάτων αλουμινίου και να προχωρήσουν σε οικομοτεχνικά βιώσιμες (βλ. τελικό κόστος προϊόντος προς τον πελάτη) αντίστοιχες γραμμές παραγωγής. Πως όμως φτιάχνεται μία σύγχρονη ζάντα αλουμινίου και πως φτάνουμε να έχουμε επί του πρακτέου τα όποια κέρδη? Μια φορά και ένα καιρό, ζάντες αλουμινίου κατασκευάζονταν και πρεσσαριστές, με την βασική δηλαδή διαδικασία που περιγράψαμε στη παράγραφο για τις ατσάλινες. Με την βελτίωση της τεχνολογίας των κατεργασιών χύτευσης σταδιακά περάσαμε στις χυτές ζάντες αλουμινίου, οι οποίες αποτελούν και την απολύτως συντριπτική πλειοψηφία των aftermarket ζαντών σήμερα.
Ας δούμε με τη σειρά τα στάδια τα οποία περνάει μία τέτοια, λιγότερο ή περισσότερο τυπική, ζάντα από τη γέννηση της μέχρι το σημείο να είναι έτοιμη να στρογγυλοκάτσει στο καλομαθημένο μουαγιέ μας. Όπως φαντάζεστε, όλα ξεκινάνε σε μία οθόνη βαρβάτου υπολογιστή. Η πρώτη φάση είναι καθαρά artistic: «ζωγραφίζονται» απλά δυσδιάστατα σχέδια που επικεντρώνονται στο αισθητικό κομμάτι του πράγματος, χωρίς για την ώρα να μπλέκουν στη κουβέντα έννοιες όπως «αντοχή» ή «βάρος». Στη συνέχεια, το αρχικό «αφηρημένο» σχέδιο μετατρέπεται σε αρχείο 3D μοντέλου. Σε αυτή τη μορφή εξυπηρετούνται δύο κατευθύνσεις: η μία αφορά τη φωτορεαλιστική πλέον απεικόνιση της ζάντας στο χώρο, όπου μπορεί το σχέδιο να κριθεί αισθητικώς πιο ζωντανά, με φίλτρα φωτισμού κλπ., ενώ η άλλη αφορά την ανάλυση του ως τώρα σχεδίου, ως προς την αντοχή του και το βάρος του μέσω των σύγχρονων μεθόδων ανάλυσης με πεπερασμένα στοιχεία (FEM - Finite Element Method). Εδώ είναι το στάδιο που, εικονικά τουλάχιστον για την ώρα, βελτιστοποιείται η τακτική «μέγιστη αντοχή από το ελάχιστο δυνατό βάρος». Αφού τελειώσει αυτό το πρώτο «θεωρητικό» κομμάτι της εξέλιξης του υποψήφιου νέου μοντέλου ζάντας και είναι έτοιμο το αρχείο για να περάσει στα ανάλογα υπολογιστικά συστήματα σχεδιασμού και κατεργασίας (CAD/CAM), σειρά έχει η δημιουργία του πρώτου χειροπιαστού, με σάρκα και οστά, πρωτότυπου της ζάντας. Το πρωτότυπο («δοκίμιο») πρέπει να περάσει από δύο κατηγορίες δοκιμών και αναλύσεων: 1ον, αντοχής σε διαφόρων ειδών καταπονήσεις και 2ον, εκτίμησης κόστους κατασκευής σε μαζική παραγωγή. Οι δοκιμές αντοχής αφορούν πλήθος διαφορετικών ειδών «κακουχιών», σκοπός των οποίων είναι να προσομοιώσουν τα ζόρια που θα φάει στο δρόμο η ζάντα μεθαύριο. Περίοπτη θέση ανάμεσα στις δοκιμές αντοχής έχουν: α, αυτή που αφορά τους κύκλους πίεσης που ασκούνται στον εξωτερικό «ώμο» της στεφάνης (προς προσομοίωση του φορτίου που ασκείται από το δρόμο κατά το στρίψιμο «με όσα» ), β, οι δοκιμές που αφορούν το φορτίο που ασκείται από το ίδιο το όχημα στο κέντρο του δίσκου μέσω της έδρασης της ζάντας στο άκρο και γ, (ίσως οι πιο σημαντικές για τις ζάντες που προορίζονται για ελληνικούς κωλόδρομους!) οι δοκιμές που αφορούν κρουστική καταπόνηση και περιλαμβάνουν απότομο χτύπημα της ζάντας από κάποιο εξωτερικό αντικείμενο. Ενώ ορισμένες από τις δοκιμές πραγματοποιούνται με τη ζάντα σκέτη, άλλες γίνονται με το ελαστικό τοποθετημένο κανονικά, ώστε να μπορεί να ελεγχθεί η πιθανότητα κατά την οποία η άσκηση φορτίου, ναι μεν δεν προξενεί μόνιμη («πλαστική») παραμόρφωση της ζάντας (δεν υπάρχει στράβωμα δηλαδή), αλλά η προσωρινή («ελαστική») παραμόρφωση να είναι σε θέση να προκαλέσει απώλεια πίεσης αέρα από το ελαστικό λόγω στιγμιαίας ανασήκωσής του από τη στεφάνη της ζάντας. Αφού όλες οι δοκιμές τελειώσουν, τα αρχικά σχέδια τροποποιούνται σύμφωνα με τα ανάλογα αποτελέσματα που προέκυψαν, νέα σχέδια γίνονται για το βελτιωμένο πρωτότυπο κ.ο.κ. από την αρχή όλη η διαδικασία μέχρι να καταλήξουν τα εμπλεκόμενα τμήματα εξέλιξης στο τελικό μοντέλο που θα πρέπει να αποστείλουν στους συναδέλφους τους στο τμήμα παραγωγής για να ξεκινήσει η μαζική κατασκευή.
Από τη παραγωγή στη κατανάλωση
Όταν λέμε ζάντα «αλουμινίου» ποτέ δεν εννοούμε ζάντα από ατόφιο αλουμίνιο. Για να καταστεί το αλουμίνιο κατάλληλο υλικό από πλευράς ιδιοτήτων αντοχής και κατεργασίας, πρέπει να αναμειχθεί με διάφορα άλλα στοιχεία (κάποια από τα συνηθέστερα είναι π.χ. χαλκός, πυρίτιο και μαγνήσιο) και να προκύψει το γνωστό μας «κράμα αλουμινίου». Η ακριβής αναλογία στοιχείων στη σύσταση του κράματος που χρησιμοποιείται σε κάθε μοντέλο ζάντας είναι από τα πλέον καλά φυλαγμένα βιομηχανικά μυστικά κάθε κατασκευαστή και αποτελεί πληροφορία που ελάχιστοι εμπλεκόμενοι γνωρίζουν, ακόμα και μέσα στο ίδιο το περιβάλλον κάθε εργοστασίου. Όποιο και να είναι το ακριβές κράμα μια χυτής ζάντας, θα πρέπει με κάποιο τρόπο να εκχυθεί στο αντίστοιχο καλούπι για να προχωρήσει η χύτευση. Τρία βασικά είδη χύτευσης μπορούν να χρησιμοποιηθούν, ανάλογα με τον τρόπο και την πίεση με την οποία εκχύνεται το λιωμένο υγρό μέταλλο στο καλούπι: χύτευση υπό την επίδραση της φυσικής βαρυτικής δύναμης μόνο (το μέταλλο εκχύνεται φυσικά στο καλούπι χωρίς περαιτέρω ασκούμενη πίεση), χύτευση υψηλής πίεσης (έμβολο υψηλής πίεσης και ταχύτητας σπρώχνει το υγρό μέταλλο στο καλούπι) και χύτευση χαμηλής πίεσης (το μέταλλο ωθείται σιγά σιγά και με μεγαλύτερη ακρίβεια, από ειδικό μείγμα αερίων προς τα καλούπι με πίεση της τάξεως των 2 bar). Οι δύο πρώτοι τύποι χρησιμοποιούνται συνήθως για το «φτηνότερο» κομμάτι της γκάμας ζαντών, ενώ η χύτευση χαμηλής πίεσης έχει επικρατήσει στους μεγάλους κατασκευαστές ζαντών για όλα τα «καλά» τους (χυτά πάντα) μοντέλα, μιας και είναι η μέθοδος που μας δίνει τις πιο ομαλές επιφάνειες (το υγρό μέταλλο ακολουθεί καλύτερα τις δυσκολότερες πτυχές του καλουπιού και ελαχιστοποιούνται τυχόν εναπομείναντες θύλακες αέρα στο χυτό). Ανάλογα με το κράμα που εκχύνεται, το ακριβές υλικό του καλουπιού και τον τύπο της χύτευσης, η θερμοκρασία του μετάλλου όταν εκχύνεται στο καλούπι βρίσκεται κοντά στους 700 oC κατά την είσοδο του και παραμένει στο καλούπι μέχρι να ψυχτεί στους 400 oC περίπου. Το καλούπι ανοίγεται και η ζάντα προχωράει στα επόμενα στάδια κατεργασίας της. Πόσα και ποια είναι αυτά? Πολλά και ποικίλα είναι η απάντηση.
Όλο το ζουμί, είτε μιλάμε για χυτή ζάντα, είτε για σφυρήλατη που θα δούμε πιο κάτω, είναι να αφαιρεθεί όλο το υλικό που μας αυξάνει το βάρος χωρίς να συνεισφέρει σε δομική αντοχή (ίσα ίσα που μπορεί, κατά περίπτωση, να την χειροτερεύει κιόλας). Σε αυτή τη κατεύθυνση οι κατασκευαστές μπορούν να καταφύγουν σε διάφορες τακτικές, όπως η δημιουργία «κούφιων» κοιλοτήτων π.χ. εντός των μπράτσων ή ακόμα και εντός των ώμων της στεφάνης πριν το χείλος. Εργαλειομηχανές ελεγχόμενες από υπολογιστικό κώδικα (π.χ. πολυαξονικές CNC φρέζες ή ανάλογοι τόρνοι), πιάνουν δουλειά και αφαιρούν κατά τόπους το «άχρηστο» υλικό (η πίσω πλευρά των μπράτσων/ακτίνων είναι από τις πιο αγαπημένες τους για φάγωμα). Στη κατηγορία αυτή υπάγεται και η κατεργασία που πολλοί γνωρίζετε ως «Flowforming» διαμόρφωση ζαντών. Αυτή αφορά την διαμόρφωση κατά πλάτος του προφίλ της στεφάνης έτσι, ώστε αυτή να αποκτά μικρότερο ή μεγαλύτερο πάχος (και πυκνότητα) με τρόπο που βελτιστοποιείται ο περιβόητος λόγος αντοχής προς βάρος: κατά το flow forming και χρησιμοποιώντας μία διάταξη σαν super high-tech τόρνο, η στεφάνη περιστρέφεται κόντρα σε κυλίνδρους κατάλληλης διαμόρφωσης, υπό τεράστιες πιέσεις και υψηλές θερμοκρασίες (300-350 oC), διαδικασία η οποία ελεγχόμενα «αδυνατίζει» το πάχος του μετάλλου και παράλληλα αυξάνει το συνολικά πλάτος της στεφάνης μέχρι το προκαθορισμένο. Με το flowforming μπορούμε να πετύχουμε πυκνότητες και ιδιότητες μετάλλου που παραδοσιακά μονάχα μέσω σφυρηλάτησης μπορούσαν να επιτευχθούν. Μείζονος σημασίας για τις τελικές ιδιότητες αντοχής του μετάλλου είναι και οι απαραίτητες θερμικές κατεργασίες στις οποίες υπόκεινται η ζάντα κατά τις σχετικές φάσεις παραγωγής της. Μετά την χύτευση ή την σφυρηλάτηση, μία ζάντα υποβάλλεται σε αύξηση της θερμοκρασίας της στους 400-600oC και μετά ψύχεται λιγότερο ή περισσότερο απότομα μέχρι τους 70 oC περίπου («ανόπτηση» ή «βαφή» αντίστοιχα), ενώ στη συνέχεια ξαναθερμαίνεται ελεγχόμενα («επαναφορά»). Όλος αυτός ο κύκλος των σκοτσέζικων ντουζ γίνεται για να ομαλοποιηθεί η κρυσταλλική δομή του μετάλλου σε όλη τη μάζα του και να αποκτήσει τον επιθυμητό συνδυασμό σκληρότητας και ολκιμότητας (ευκαμψίας). Οι ακριβείς θερμοκρασίες κάθε φάσης της θερμικής επεξεργασίας είναι τόσο σημαντικές, ώστε παρέκκλιση ελάχιστων βαθμών πιο πάνω ή πιο κάτω από το προβλεπόμενο να μας δώσει υλικό με ψαθηρότητα πέραν του επιτρεπτού και να χρειαστεί να ξαναλιώσει ως άχρηστο.
Τελειώσαμε? Όχι βέβαια. Η ζάντα δεν πρέπει να μασάει από υγρασίες και άλλους περιβαλλοντικούς παράγοντες που μπορεί π.χ. να την διαβρώσουν, οπότε στο παιχνίδι μπαίνουν πλέον οι ηλεκτροχημικές κατεργασίες που προσδίδουν στρώματα προστατευτικών επιφανειών στο μέταλλο, όπως είναι π.χ. η ανοδίωση. Ακολούθως, σειρά παίρνουν επιστρώσεις όπως οι ειδικές βαφές ανάλογα με το τελικό χρώμα που θέλουμε να προσδώσουμε, η εποξική σκόνη επικάλυψης και τα διάφορα βερνίκια. Ανάλογα τώρα με το αν στην τελική επιφάνεια της ζάντας ο κατασκευαστής θέλει να δώσει γυαλάδα επιπέδου καθρέπτη για ξύρισμα ή περισσότερο ματ υφή (που είναι και της μόδας), έχουν προηγηθεί οι σχετικές κατεργασίες π.χ. ειδικής αμμοβολής με μεταλλικά ή και κεραμικά σφαιρίδια. Ζάντες στο σχέδιο των οποίων περιλαμβάνονται απότομες ακμές και γωνίες (π.χ. στις άκρες των μπράτσων τους), κατά κανόνα έχουν περάσει και από τοπική κοπή-φρεζάρισμα με διαμάντι. Μετά από όλα αυτά, τώρα ξέρετε γιατί έπρεπε να σκάσετε ένα κάρο λεφτά πέρσι για τις φοβερές και τρομερές 19άρες σας.
Οι σούπερ σπέσιαλ κατηγορίες
Όσα λεφτά και να σκάσατε πέρσι λοιπόν για ζάντες, δεν θα έπρεπε να ντρέπεστε που είναι κατασκευασμένες από το ίδιο υλικό βάσης με το κουτάκι του αναψυκτικού στο ψυγείο του περιπτερά απέναντι? Μία ζάντα αλουμινίου, όσες κατεργασίες και να περάσει, στο τέλος της ημέρας δεν παύει να παραμένει μία ζάντα αλουμινίου. Επομένως, είναι ώρα να γίνουμε λίγο πιο σνομπ με το χυτό αλουμίνιο και να χοντρύνουμε το παιχνίδι βλέποντας τι γίνεται με κάποιες πιο εξειδικευμένες κατηγορίες ζαντών, τις ζάντες για πολύυυυυυυ βαθιά πορτοφόλια.
Μαγνησίου:Το μαγνήσιο σαν στοιχείο έχει 35% μικρότερη πυκνότητα από το αλουμίνιο και αυτό αντίστοιχα αντικατοπτρίζεται στο βάρος μίας κατηγορίας ζαντών-φετίχ για οποιονδήποτε ονειρεύεται να κάνει το καμάρι του ένα «αγωνιστικό δρόμου». Στη πραγματικότητα και μετά από όλες τις επιστρώσεις, κατεργασίες, προσμίξεις κραμάτων, το κέρδος με μία ζάντα μαγνησίου σε απόλυτο βάρος δεν φτάνει αυτό το θεωρητικό 35% σε σχέση με μία αλουμινίου ίδιας διάστασης, αλλά το 15-20%, το οποίο σε καμία περίπτωση φυσικά δεν είναι αμελητέο. Οι ζάντες μαγνησίου δεν είναι καμία καινούργια εφεύρεση των τελευταίων ετών, κάθε άλλο, αφού χρονικά προηγούνται των αντίστοιχων αλουμινίου. Χυτές ζάντες μαγνησίου ξεκίνησαν να παράγονται πριν σχεδόν εκατό χρόνια για αγωνιστικά αυτοκίνητα, αλλά αντιμετώπιζαν διάφορα προβλήματα και από το 1960 και μετά οι αντίστοιχες αλουμινίου πήραν τα σκήπτρα. Το αρχικό πρόβλημα ήταν η έλλειψη των κατάλληλων κραμάτων μαγνησίου που θα έλυναν όλα τα «κουσούρια» που παρουσίαζε η χρήση ατόφιου μαγνησίου: διάβρωση, ρωγμές και καύση! Το μαγνήσιο, χωρίς να είναι εύφλεκτο, από τη στιγμή που αρχίσει να καίγεται θέλει τρία Canadair για να σβήσει. Στη πορεία του χρόνου ωστόσο, όλα γύρισαν τούμπα, αφού εξελίχτηκαν σύγχρονα κράματα μαγνησίου τα οποία όχι μόνο έλυσαν τα προαναφερθέντα προβλήματα, αλλά κατέστησαν τις ανάλογες ζάντες τα απόλυτα τέρατα αντοχής και παράλληλης εξοικονόμησης βάρους. Λόγω τους εξωφρενικού τους κόστους απαντώνται κυρίως σε αγωνιστικά αυτοκίνητα και οι περιπτώσεις χρήσης τους ως OEM σε εργοστασιακά αυτοκίνητα είναι ελάχιστες (π.χ. Porsche Carrera GT, Lotus Esprit Sport 350, Ferrari F355, DeTomaso Pantera, Lamborghini Diablo SE30/GTR, Corvette C5 ως εξτρά). Μία ζάντα μαγνησίου, όπως και μία αλουμινίου μπορεί να είναι είτε χυτή είτε...
Σφυρήλατες: Κατά την σφυρηλάτηση, αντί να αφήσουμε το μέταλλο να «δέσει από μόνο του» στο καλούπι όπως ουσιαστικά συμβαίνει με την χύτευση, το αναγκάζουμε να ακολουθήσει «με το ζόρι» την μήτρα του καλουπιού στο οποίο το πιέζουμε («σφυρηλατούμε»). Το κομμάτι του μετάλλου πριν την σφυρηλάτηση θερμαίνεται στους 400oC (βρίσκεται σε μαλακότερη μεν αλλά σε στερεή ακόμα δε μορφή) και στη συνέχεια τοποθετείται σε πρέσες που μπορούν να πλησιάσουν σε πίεση και τους 10.000 τόνους. Η διαμόρφωση του σχήματος της ζάντας δεν γίνεται μια κι έξω, αλλά σε διαδοχικά στάδια σφυρηλάτησης μέχρι να πάρει την τελική του μορφή, με το κομμάτι να ξαναθερμαίνεται ανάμεσα στα διάφορα στάδια. Με την όλη αυτή διαδικασία, η μοριακή κρυσταλλική δομή του μετάλλου αποκτά μεγαλύτερη «πυκνότητα», τα χαρακτηριστικά αντοχής του μετάλλου είναι περισσότερο ομοιόμορφα σε όλη την μάζα του κομματιού (κάτι που δεν μπορεί να επιτευχθεί στον ίδιο βαθμό με τη χύτευση, αφού εκεί κατά την πήξη το μέταλλο αποκτά ιδιότητες με μεγαλύτερο εύρος -ανάλογα με τη θέση του στο καλούπι) και έτσι τελικά παίρνουμε έναν ελαφρύτερο και ανθεκτικότερο τροχό. Το κόστος παραγωγής είναι μεγαλύτερο από το αντίστοιχο των χυτών ζαντών και φυσικά αυτό βγαίνει άμεσα στη τιμή λιανικής που θα σας ζητήσουν για μία σφυρήλατη ζάντα. Ιδιαίτερη διευκρίνηση θέλει το γεγονός ότι ως «σφυρήλατες» στο εμπόριο κυκλοφορούν όχι μόνο όσες ζάντες είναι ολόκληρες σφυρήλατες, αλλά και όσες έχουν μόνο σφυρήλατο δίσκο/κέντρο ή μόνο στεφάνη (αυτό αφορά κυρίως τις διαιρούμενες ζάντες με βιδωτό κέντρο στη στεφάνη και όχι τις μονομπλόκ). Μιλώντας για διαιρούμενες ζάντες, αξίζει να χει κάποιος στο νου του ότι υπάρχουν πολλοί διαφορετικοί συνδυασμοί τύπου στεφάνης-δίσκου στο εμπόριο: μπορεί π.χ. μία διαιρούμενη ζάντα να έχει χυτό δίσκο και flow forming στεφάνη ή σφυρήλατο δίσκο και χυτή ή flow forming στεφάνη.
Carbon: Και ερχόμαστε στη κατηγορία των ζαντών που ήρθε πολύ πρόσφατα στο aftermarket προσκήνιο, τις ανθρακονημάτινες. Τέσσερις-πέντε μικρές εταιρίες (η γνωστότερη εκ των οποίων φαλίρισε και εξαγοράστηκε...) είναι αυτές που μέχρι τώρα έχουν προσφέρει ανάλογες λύσεις, σε τιμές που η τετράδα γλύφει ή και ξεπερνάει χαλαρά σε τιμή το πενταψήφιο ποσό. Για τα πλεονεκτήματα των ανθρακονημάτων και γενικότερα των σύνθετων υλικών έχουμε αναλυτικά ασχοληθεί στο παρελθόν, οπότε σας παραπέμπω στα αντίστοιχα Know How των τευχών εκείνων. Αρχικά, στην αγορά είχαν κυκλοφορήσει ζάντες με ανθρακονημάτινη στεφάνη μόνο και (κατά κανόνα) κέντρο μαγνησίου, ενώ τα τελευταία 2-3 χρόνια κυκλοφόρησαν και κάποιες φουλ μονομπλόκ κάρμπον. Δεν υπάρχει αμφιβολία ότι οι εν λόγω ζάντες είναι το τοπ αυτή τη στιγμή ως προς το κέρδος σε βάρος και μόνο, όμως, και για την ώρα, τα πλεονεκτήματα σταματούν κάπου εδώ. Η αντοχή τους σε κρουστική καταπόνηση είναι «αμφισβητούμενη» (αν ψάξετε στο internet θα βρείτε όμορφες φωτογραφίες με μπράτσα carbon ζαντών κομμένα σαν αγγούρι) λόγω της φύσεως του υλικού σε σχέση με τα πιο «ανεκτικά» σε παραμόρφωση μέταλλα, ενώ αν π.χ. στην όπισθεν γδαρθούν στο πεζοδρόμιο δεν θα στην φτιάξουν στην Καβάλας με 50 ευρώ. Δεν είναι τυχαίο, ότι μέχρι ώρας κανένας από τους μεγάλους κατασκευαστές ζαντών δεν έχει ασχοληθεί ακόμα σοβαρά με το θέμα: η προσωπική γνώμη του γράφοντος είναι ότι δεν αξίζει κάποιος ακόμα να προχωρήσει σε μία τέτοια επένδυση, εκτός και είναι υπεράρρωστος κοντράκιας, το αυτοκίνητο δεν το στρίβει καθόλου και το βγάζει από το γκαράζ μόνο για κόντρες του 3χίλιαρου. Δεν ξέρω και πολλούς τέτοιους πλέον... Ναι, έχουν μέλλον (οι κάρμπον ζάντες, όχι οι κοντράκηδες του 3χίλιαρου), αλλά ακόμα είναι νωρίς, θα πρέπει να βελτιωθούν οι μέθοδοι κατασκευής σε πιο μαζικό επίπεδο για να πέσουν κιόλας παράλληλα κι οι τιμές τους. Εν κατακλείδι, Αν κάποιος θέλει να τα σκάσει χοντρά, του συνιστώ να συνεχίζει να παίζει στις δύο προηγούμενες κατηγορίες ειδικών ζαντών που είδαμε και να αφήσει τις carbon μαγκιές για αργότερα.
Ανάμεσα στη ζαντούλα μας και το δρόμο...
...όμως είναι τα λάστιχα. Εξειδικεύσαμε σήμερα τη κουβέντα στη ζάντα, ωστόσο το κεφάλαιο «τροχός» δεν πάει πουθενά χωρίς το έτερον ήμισυ του σώτρου: το επίσωτρο! Ναι, στα ελαστικά αναφερόμαστε και είναι αυτά τα οποία θα μονοπωλήσουν κατά βάση το ενδιαφέρον μας από τον επόμενο μήνα, ο οποίος καλώς ή κακώς εχόντων των πραγμάτων, θα μας βρει με κούρεμα στα ομόλογα και τους μισθούς αλλά ποτέ των ποτών στο Know How. Εκεί δεν δεχόμαστε σκόντο…
Αρθρογράφος
Δοκιμές Αυτοκινήτου CarTest.gr
Θεαματική συμμετοχή δύο αγωνιστικών αυτοκινήτων της Nissan στο Ιστορικό Ράλι Ακρόπολις.