ΤΡΟΧΟΙ PART III
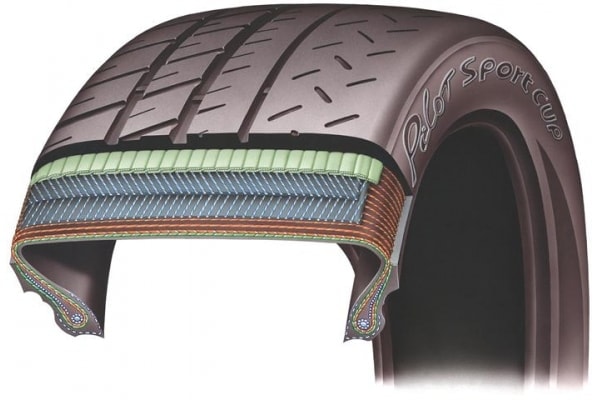
Το Α και το Ω
Τα βλέπουμε τόσο συχνά σε «χαμαλοδουλειές» (πλαϊνά βαρκών, στοιβαγμένα σε πιθανά σημεία εξόδου στις πίστες, γεμισμένα με τσιμέντο σε ρόλο βάσεις για διάφορες πινακίδες, σε κούνιες και όπου αλλού δε μπορεί να φανταστεί ακόμα και το πιο άρρωστο μυαλό), που συχνά ξεχνάμε τον θεάρεστο και αγαθοεργή ρόλο του ελαστικού στη λειτουργία και την κίνηση ενός αυτοκινήτου. Αν το σκεφτεί κανείς λίγο σουρεάλ, τι να τις κάνεις τις ρουλεμανάτες billet τουρμπίνες, τις 40πίστονες μονομπλόκ δαγκάνες ή τα γόνατα ανάρτησης με τις 82 ρυθμίσεις, αν όλα αυτά δεν μπορούν να επιδείξουν το έργο τους στο δρόμο κατά το δοκούν: όλα ανεξαιρέτως αυτά τα φοβερά και τρομερά υποσυστήματα ενός αυτοκινήτου, τα κάνει μάγκες αυτό το μαύρο, καλομοίρικο και φαινομενικά απλό από πλευράς πολυπλοκότητας κατασκεύασμα, το ελαστικό του τροχού. Είτε το αυτοκίνητο σας κοστίζει τριακόσια χιλιάρικα είτε τρία, είτε αυτό κάνει το 0-100 σε 5 δευτερόλεπτα είτε το κάνει σε δέκα λεπτά, η ουσιαστική επαφή του με τον έξω κόσμο (=δρόμος!), είναι σε κάθε περίπτωση τέσσερις μικρές σχετικά διεπιφάνειες εδάφους-λάστιχου, όχι πολύ μεγαλύτερες ή μικρότερες –αναλόγως- από την παλάμη σας. Για δεδομένο οδόστρωμα λοιπόν, όλο το παιχνίδι μεταφέρεται στο έτερον μισό της εξίσωσης που δεν είναι άλλο από το λάστιχο. Αφού είδαμε τους δύο προηγούμενους μήνες το πρώτο συνθετικό του «ζαντολάστιχου», σειρά έχει το δεύτερο, φύγαμε.
Μια σύντομη αναδρομή
Η σύλληψη της ιδέας ενός ελαστικού για τους τροχούς ενός οχήματος φουσκωμένου με αέρα («πνευματικό ελαστικό») και όχι από μασίφ στέρεο υλικό έχει ηλικία περίπου ενάμιση αιώνα, όσο περίπου και το αυτοκίνητο με μηχανή εσωτερικής καύσης. Οι πρώτες πατέντες κατατέθηκαν στα μέσα του 19ου αιώνα, το 1888 ο Σκοτσέζος John Dunlop λάνσαρε το πρώτο πνευματικό λάστιχο για ποδήλατα, αλλά πρέπει να φτάσουμε στο 1895 και τον Michelin για να μιλήσουμε για το πρώτο πνευματικό ελαστικό αυτοκινήτου. Το 1908 ιδρύεται ο βάζελος και ταυτόχρονα τα πρώτα ελαστικά με χάραξη στο πέλμα, ενώ δυο χρόνια αργότερα τα ελαστικά παίρνουν το μαύρο χρώμα (από λευκά) που ξέρουμε σήμερα, με την προσθήκη μαύρου άνθρακα. Το 1937, εμφανίστηκαν στο εμπόριο τα πρώτα ελαστικά από συνθετική γόμα (μέχρι τότε ως βάση είχαν το φυσικό καουτσούκ) και σχεδόν δέκα χρόνια αργότερα, η Michelin βγάζει το πρώτο radial ελαστικό του οποίου τα πλεονεκτήματα θα δούμε αμέσως παρακάτω. Μέχρι τώρα, όλες οι εξελίξεις που αναφέραμε αφορούσαν ελαστικά με σαμπρέλα, μιας και μόλις το 1947 η BFGoodrich ανακοίνωσε ελαστικά άνευ σαμπρέλας («tubeless»). Τα αγαπημένα μας χαμηλοπρόφιλα ελαστικά, έκαναν τα πρώτα τους δειλά βήματα τη δεκαετία του ’70, ενώ από εκεί και μετά, παρόλο που στη βασική κατασκευαστική μορφή των ελαστικών δεν είχαμε κοσμογονικές αλλαγές, το παιχνίδι μεταφέρθηκε περισσότερο στη χημεία των συνθέσεων όλο και αποδοτικότερων, από πλευράς επιδόσεων, συστάσεων γόμας, στην τριβολογία και τις νόρμες θορύβου, άνεσης και κατανάλωσης. Οι κατασκευαστές ελαστικών έχουν φτάσει σήμερα να προσφέρουν μία τεράστια γκάμα από προϊόντα, που παντρεύουν -ομολογουμένως εντυπωσιακά- επιτυχώς τα φαινομενικά ασυμβίβαστα (π.χ. από ένα ελαστικό για χαμηλή κατανάλωση καυσίμου, δεν μπορούμε να περιμένουμε και βέλτιστα επίπεδα πρόσφυσης και αντιστρόφως), έτσι ώστε να μπορούμε να πούμε με ασφάλεια ότι ένα σημαντικό κομμάτι της τεχνολογίας που κουβαλάει ένα σύγχρονο αυτοκίνητο, βρίσκεται καλά κρυμμένο στις τέσσερις λαστιχένιες άκρες του.
Μαθήματα ανατομίας: ένα κυλινδρικό κομμάτι λάστιχο?
Έτσι φαίνεται αρχικά, αλλά όποιος τυχόν μείνει εκεί, πλανάται πλάνη οικτρά. Όπως είπαμε, ολόκληρο το όχημα εναποθέτει όλες του τις ελπίδες, σε στροφές και ευθείες, στα ελαστικά, τα οποία με τη σειρά τους δεν είναι και το πιο φτηνό ανταλλακτικό πάνω στο αυτοκίνητο. Οπότε, δεν μπορεί, μία Χ τεχνολογία πάνω τους, βρε αδερφέ, δεν θα την έχουν? Την έχουν και την παραέχουν. Για να δει κάποιος κανονικά τι κρύβει στα σωθικά του ένα ελαστικό, θα πρέπει ή να το σφάξει με μαχαίρι ή να κάνει ένα βαρβάτο burn-out, όμως εμείς εδώ για πάρτη σας, θα το καταφέρουμε εντελώς αναίμακτα και φιλειρηνικά. Το βασικό δομικά μέρος ενός ελαστικού είναι ο σκελετός του, τα λεγόμενα και «λινά» (κατά το γνωστό «βγήκε ο κάφρος με τα λινά από τη πίστα» κτλ.).
Στα παραδοσιακά «old school» ελαστικά, ο σκελετός αποτελείται από διαδοχικά στρώματα παράλληλων ενισχυμένων υφασμάτινων ινών (αρχικά από βαμβάκι, αργότερα από rayon, nylon, πολυεστέρα), οι οποίες διατρέχουν διαγώνια το ελαστικό κατά πλάτος από άκρη σε άκρη του, δηλαδή στρώσεις σε διάφορες «λοξές» γωνίες ως προς τον διαμήκη άξονα κίνησης του τροχού. Κάθε στρώμα εξ’ αυτών καλύπτεται από κάποιο μίγμα γόμας (περισσότερα για τη σύσταση της γόμας πιο κάτω), ενώ στις δύο άκρες του (στο εσωτερικό και εξωτερικό χείλος του ελαστικού που ακουμπάει στη ζάντα) τυλίγεται κάθε στρώμα γύρω από ένα πλαστικοποιημένο δακτύλιο από ατσάλι υψηλής αντοχής, επικαλυμμένο με κράμα χαλκού για προστασία από διάβρωση. Οι δύο αυτοί εσωτερικοί περιφερειακοί δακτύλιοι (δείτε και το συνοδευτικό σχήμα), ουσιαστικά συγκρατούν το ελαστικό πάνω στη στεφάνη της ζάντας και ούτε λίγο, ούτε πολύ, αποτελούν το θεμέλιο κάθε ελαστικού ως προς την έδραση του στο συγκρότημα του τροχού. Η δομή σκελετού που περιγράψαμε, είναι το χαρακτηριστικό των «cross-ply» ελαστικών, τα οποία ονομάζονται έτσι ακριβώς λόγω του γεγονός ότι οι ίνες τους διασταυρώνονται σε διάφορες γωνίες εκατέρωθεν του άξονα συμμετρίας του ελαστικού. Σήμερα, και όσον αφορά τα επιβατικά αυτοκίνητα για δρομίσια χρήση τουλάχιστον, τα cross-ply έχουν αντικατασταθεί από τα γνωστά σε όλους radial («ακτινωτά») ελαστικά.
Η διαφορά στα radial έγκειται στην διάταξη των (κατά βάση ενισχυμένων με ατσάλι) «καλωδίων» του σκελετού: εδώ οι ίνες είναι παράλληλες μεταξύ τους (δεν διασταυρώνονται) και είναι τοποθετημένες σε κάθετη γωνία (90 μοιρών) ως προς τον διαμήκη άξονα του ελαστικού. Το γεγονός ότι στα radial ελαστικά οι ίνες μεταξύ τους δεν μπλέκουν τα μπούτια τους, όπως στα cross-ply, αυτόματα συνεπάγεται μικρότερες εσωτερικές τριβές, που με τη σειρά τους σημαίνουν μικρότερη τριβή κύλισης (περισσότερα για αυτή αργότερα) και εν τέλει μικρότερες απώλειες (ισχύος ή κατανάλωσης καυσίμου, ανάλογα από ποια πλευρά το βλέπει κανείς...) από ένα cross ply ελαστικό.
Μετά τον σκελετό και πριν φτάσουμε στο πέλμα, συναντάμε ανάμεσα τους το δεύτερο κύριο κομμάτι ενός ελαστικού, τη «ζώνη». Μία, δύο ή περισσότερες ζώνες (τα off-road ελαστικά μπορεί να διαθέτουν ακόμα και πέντε) διαθέτουν όλα τα radial ελαστικά, αλλά αντιθέτως, ορισμένα μόνο από τα cross-ply (τα ονομαζόμενα και «belted bias»). Μία ζώνη radial ελαστικού αποτελείται παραδοσιακά από πυκνές παράλληλες ίνες χάλυβα, ενώ για έξτρα αντοχή μπορεί να συμπληρώνεται από επιπλέον στρώματα από nylon ή ακόμα και Kevlar (αραμίδι!) σε κάποια εξειδικευμένα και πανάκριβα ελαστικά (βλ. Lamborghini LM002). Το κομμάτι των ζωνών του ελαστικού παίζει μείζονα ρόλο στην μεταφορά της ροπής από το πέλμα προς τα λινά και viceversa, προσθέτει ανθεκτικότητα στα επίπεδα αντοχής ολόκληρου του ελαστικού (π.χ. από κοψίματα, που χωρίς την παρουσία τους θα διαπερνούσαν το πάχος του) διαθέτοντας ταυτόχρονα την ευκαμψία που απαιτείται για την απορρόφηση κραδασμών από της ανωμαλίες του οδοστρώματος.
Πριν φτάσουμε στο πέλμα του ελαστικού, πρέπει να αναφέρουμε δύο άλλα από τα καθαρά «λαστιχένια» του κομμάτια. Το πρώτο είναι τα λεγόμενα «πλαϊνά», το μέρος που εκτείνεται από το πέλμα μέχρι τον δακτύλιο που πιάνει στο χείλος της ζάντας. Τα πλαϊνά δεν διαθέτουν εσωτερικά τις βαρβάτες ενισχύσεις που είδαμε ότι διαθέτει το κεντρικό κομμάτι του ελαστικού, με τις ζώνες του και τα ρέστα, όμως σε κάθε περίπτωση το πάχος των επιστρώσεων γόμας σε αυτό το σημείο, πρέπει αφενός να είναι σε θέση να υπερνικά εξωτερικές καταπονήσεις, όπως αιμοβόρικα πεζοδρόμια και αφετέρου να μπορεί να «σφραγιστεί» κατά την παραγωγή με όλα εκείνα τα μύρια νούμερα, γράμματα και λογότυπους που συναντάμε στο πλαϊνό των ελαστικών (τα πιο «Power» εκ των οποίων θα αναλύσουμε σε επόμενη συνέχεια μας). Επίσης, έχουμε και την εσωτερική επίστρωση (εδώ χρησιμοποιείται γόμα βουτυλίου συν ένα κάρο ειδικά πρόσθετα), που ενώ είναι το λείο μέρος του ελαστικού, που μόνο ο υπό πίεση αέρας ανάμεσα σε αυτό και τη ζάντα κανονικά αντικρίζει, εντούτοις έχει αναλάβει την σημαντική δουλειά να κρατάει ακριβώς αυτόν τον υπό πίεση αέρα καλά φυλακισμένο στο χώρο του και να μην δραπετεύει προς τα λινά. Τα radial ελαστικά (είτε μιλάμε για street είτε για drag radials) μπορεί γενικώς να θεωρούνται πλέον ως πανάκεια σήμερα, και δικαίως λόγω των συνολικών βέλτιστων χαρακτηριστικών πρόσφυσης, αντίστασης κύλισης και αντοχής πέλματος που προσφέρει ο συνδυασμός ακτινικού σκελετού και των «επικουρικών» ζωνών, αλλά αξίζει να αναφέρουμε πως η διαγώνια διάταξη των ινών των παραδοσιακών cross-ply ελαστικών υπερισχύει στην ανθεκτικότητα των πλαϊνών και επίσης στην διαχείριση πολύ μεγάλων κάθετων φορτίων (φορτηγατζήδες, παρακαλώ ένα βήμα μπροστά).
Παιδί για όλες τις δουλειές: το πέλμα
Το κομμάτι του ελαστικού που αφήσαμε τελευταίο στην κουβέντα περί ανατομίας του, είναι το πέλμα, δηλαδή το μέρος εκείνο που παίρνει στις πλάτες του την τελική επαφή μεταξύ δρόμου και ολόκληρου του τροχού και κατ’ επέκταση όλου του οχήματος. Σήμερα εδώ, δεν θα ασχοληθούμε με τη σύσταση της γόμας του ως προς την επίδραση αυτής στα χαρακτηριστικά πρόσφυσης (αυτό θα γίνει νεξτ μάνθ, πακέτο με τριβές και άλλα ωραία φυσικομαθηματικά), αλλά περισσότερο με το γεωμετρικό και σχεδιαστικό κομμάτι του πέλματος. Για να είμαστε σαφείς εξ’ αρχής λοιπόν, το πέλμα επηρεάζει αθροιστικά όσο τίποτα άλλο την κατευθυντικότητα, την πρόσφυση, την άνεση, το επίπεδο θορύβου, την κατανάλωση και την συμπεριφορά στο βρεγμένο. Μπορεί όλα αυτά τα χαώδη σχέδια, που βλέπουμε σε απίστευτη ποικιλία ανά κατασκευαστή και μοντέλο, να μην βγάζουν και πολύ νόημα αρχικά ως προς τη λειτουργία τους και να μένουμε να τα χαζεύουμε αισθητικά (αν και πλάκα πλάκα οι κατασκευαστές κάνουν έρευνες και για αυτό το κομμάτι, πως χτυπάει δηλαδή το σχέδιο του πέλματος στο μάτι), όμως στη πραγματικότητα όλα παίζουν το δικό τους ξεχωριστό ρόλο. Πάμε να τα δούμε ένα-ένα:
Blocks: Ονομάζονται τα «τετραγωνάκια» (ή ρόμβοι κατά περίπτωση) που συναντάμε στο κεντρικό κομμάτι πέλματος και από τα οποία αριστερά – δεξιά – εμπρός - πίσω τους υπάρχει αυλάκωση. Αποτελούν το μεγαλύτερο κομμάτι της επιφάνειας του πέλματος και παρέχουν το βασικό ποσοστό της παραγόμενης πρόσφυσης.
Πλευρά: Οι λείες λωρίδες γόμας που σχηματίζουν μια ευθεία «ζώνη» σε όλο το μήκος της περιφέρειας του πέλματος, ονομάζονται «πλευρά». Σε χειμερινά ή βρόχινου προσανατολισμού ελαστικά, μπορεί να μην υπάρχουν καν στο πέλμα.
Αυλακώσεις: Οι αυλακώσεις έχουν να κάνουν με την ικανότητα διαχείρισης των ποσοτήτων νερού που μπορεί να απομακρύνει το ελαστικό στο πέρασμα του από βρεγμένες επιφάνειες και να τις κατευθύνει από το εμπρός μέρος του στο πίσω, διατηρώντας έτσι την επαφή του με το οδόστρωμα και αποφεύγοντας την δημιουργία του φαινομένου της «υδρολίσθησης». Ο λόγος της συνολικής επιφάνειας των αυλακώσεων ενός πέλματος, προς την συνολική επιφάνεια των blocks και των πλευρών του, φανερώνει το πόσο βρόχινο ή στεγνό προσανατολισμό έχει το ελαστικό: τα γνωστά «χειμερινά» ελαστικά έχουν μεγάλο τέτοιο λόγο, τα λεγόμενα «καλοκαιρινά» ή «ελαστικά επιδόσεων» έχουν πολύ μικρότερο, ενώ οι αγωνιστικές σλικαδούρες μηδενικό.
Σχισμές: Οι εγκάρσιες ή διαγώνιες σχισμές, αφενός επιτρέπουν στα blocks του πέλματος να καμφθούν ελεύθερα και αφετέρου, ανάλογα με τη σχεδίαση του πέλματος, να “γεμίζουν” τις μεγαλύτερες κεντρικές περιφερειακές αυλακώσεις με νερό, υποβοηθώντας τη ροή που σχηματίζεται. Επίσης, δημιουργούν απότομες ακμές στο σχήμα του πέλματος, γεγονός που αυξάνει τη πρόσφυση («γάτζωμα») του ελαστικού, κυρίως σε πάγο, χιόνι και χώμα.
Λακκάκια: Συνήθως βρίσκονται στις εξωτερικές πλευρές του πέλματος κάποιων ελαστικών και υποβοηθούν στην αποβολή θερμότητας (υπομονή ένα μήνα για συζήτηση περί θερμοκρασίας).
Ώμοι: Είναι τα δύο καμπυλοειδή κομμάτια που ενώνουν το πέλμα με τα δύο πλαϊνά του ελαστικού και είναι αυτά που εξασφαλίζουν ότι το ελαστικό δεν θα χάσει επαφή με το οδόστρωμα κατά τους ελιγμούς και τις πλευρικές φορτίσεις.
Ανάλογα τώρα με το πως όλα τα παραπάνω διανέμονται ως προς τον διαμήκη άξονα συμμετρίας του πέλματος, ξεχωρίζουμε τα ελαστικά σε:
Συμμετρικά: Ο πιο απλός τύπος και αυτός που βρίσκουμε συνήθως σε νορμάλ αυτοκίνητα, με νορμάλ οδηγούς, με νορμάλ πορτοφόλι: το σχέδιο του πέλματος είναι ομοιόμορφο εκατέρωθεν του άξoνα συμμετρίας που χωρίζει κατά πλάτος το πέλμα στα δύο μισά του.
Ασύμμετρα: Εδώ η κατάσταση είναι πιο σύνθετη και το σχέδιο αλλάζει κατά πλάτος του πέλματος. Συνήθως, η εξωτερική πλευρά ενός ασύμμετρου ελαστικού έχει λιγότερες και μικρότερες αυλακώσεις, αφού σε αυτή πέφτει το περισσότερο βάρος κατά την πλευρική καταπόνηση και η εσωτερική περισσότερες, για να μην έχουμε παρατράγουδα αν κάτσει και λίγο λιμνάζων νεράκι.
Ομοιοκατευθυνόμενα: Τα ασύμμετρα πέλματα είναι συνήθως και ομοιοκατευθυνόμενα (unidirectional), δηλαδή έχουν σχεδιαστεί για να γυρίζουν σε συγκεκριμένη φορά περιστροφής ως προς την κίνηση του οχήματος, κάτι που βοηθάει στις επιδόσεις ευθείας (επιτάχυνσης ή επιβράδυνσης). Αν ένα ελαστικό είναι ομοιοκατευθυνόμενο, αλλά συμμετρικό, πρέπει να τοποθετηθεί με συγκεκριμένη φορά μεν, αλλά σε οποιαδήποτε από τις δύο (δεξιά ή αριστερή) πλευρά του αυτοκινήτου. Αν όμως είναι ασύμμετρο ομοιοκατευθυνόμενο, τότε θέλει και συγκεκριμένη φορά και πλευρά κατά την τοποθέτηση. Στη πρώτη περίπτωση στο πλαϊνό αναγράφεται μόνο η σωστή φορά (με ένα σχετικό βελάκι) ενώ στη δεύτερη χαρακτηρίζεται καταλλήλως και η «έξω» πλευρά.
Βαλκανιζατέρ με ή χωρίς αμορτισέρ
Ας δούμε λίγα πράγματα και γύρω από την ενδιαφέρουσα διαδικασία κατασκευής ενός τυπικού ελαστικού. Περίπου 1 δισεκατομμύριο ελαστικά κατασκευάζονται παγκοσμίως το χρόνο, σε 500 περίπου συνολικά εργοστάσια, οπότε όπως καταλαβαίνετε, η όλη διαδικασία από την αρχή μέχρι το τέλος είναι απολύτως αυτοματοποιημένη. Πρώτο στάδιο είναι η μίξη των διαφόρων συστατικών, ώστε να προκύψει το τελικό μείγμα της γόμας που θα χρησιμοποιηθεί τόσο στα αντίστοιχα εξωτερικά κομμάτια (πέλμα, εσωτερική επίστρωση και πλαϊνά), όσο και εσωτερικά ως επικάλυψη π.χ. των διαφόρων στρωμάτων λινών.
Τα συστατικά αυτά που αναμειγνύονται, ξεκινάνε από φυσικό καουτσούκ και διάφορα συνθετικά πολυμερή λάστιχα με ονομασίες-σιδηρόδρομους οι οποίες κάπου στα συνθετικά τους περιέχουν βουτύλια, βουτάνια και στυρένια, μαύρο άνθρακα, ο οποίος εκτός από το χρώμα, προσδίδει αντιχαρακτικές ιδιότητες στη γόμα, πυρίτιο, το οποίο επηρεάζει τα θερμοκρασιακά χαρακτηριστικά του ελαστικού, θείο, το οποίο είναι απαραίτητο για τη διαδικασία του βουλκανισμού που θα αναφέρουμε παρακάτω και ένα κάρο διάφορα άλλα χημικά, όπως καταλύτες και πρόσθετα, καθένα από τα οποία είναι απαραίτητο για το τελικό προϊόν. Φυσικά, η ακριβής σύσταση και αναλογία διαφέρει ανάλογα με τις ιδιότητες της γόμας που θέλουμε σε κάθε μοντέλο και ανάλογα με την χρήση και τον τύπο του ελαστικού.
Η μίξη γίνεται σε μηχανήματα με ειδικούς περιστρεφόμενος ρότορες και απώτερος σκοπός είναι η ομογενοποίηση του μείγματος στο μέγιστο δυνατό βαθμό, ώστε να αποκτήσει ίδιες ιδιότητες σε όλη του τη μάζα. Επόμενο στάδιο είναι η ετοιμασία των επιμέρους ξεχωριστών στρωμάτων που απαρτίζουν το ελαστικό. Τα κομμάτια από γόμα περνάνε με τη διαδικασία της εξέλασης μέσα από κατάλληλα καλούπια για να πάρουν το επιθυμητό προφίλ και στη συνέχεια περνάνε από τη διαδικασία που έχετε ακούσει ως «βουλκανισμό». Ο βουλκανισμός, περιλαμβάνει την ένωση των μονομερών μορίων του μείγματος της γόμας σε μακρύτερες αλυσίδες (πολυμερισμός), παρουσία θείου και υπό συγκεκριμένες συνθήκες υψηλής θερμοκρασίας, σε ειδικούς φούρνους. Στη συνέχεια το προφίλ ψύχεται και κόβεται κατάλληλα για το επόμενο στάδιο.
Σε άλλα μηχανήματα «πλέκονται» τα στρώματα του σκελετού (υφασμάτινα και ατσάλινα) και των ζωνών. Το επόμενο στάδιο περιλαμβάνει την εναπόθεση των προαναφερθέντων στρώσεων γόμας, σκελετού και ζωνών κατά σειρά σε τύμπανα, ώστε να αρχίσει να διαμορφώνεται το συνολικό προφίλ του ελαστικού. Οι άκρες τυλίγονται κατάλληλα, ώστε με την προσθήκη των ενισχυτικών δακτυλίων να σχηματιστούν τα χείλη που θα πιάσουν στη ζάντα.
Ακολούθως, όλο αυτό το πακέτο που σχηματίστηκε στο τύμπανο, περνάει από διαδικασία βουλκανισμού (σκλήρυνσης του πολυμερούς) σε θερμοκρασίες κοντά στους 180 βαθμούς Κελσίου και κοντά στα 350psi πίεση ώστε να «παντρευτούν» μεταξύ τους σωστά, όλα τα επιμέρους στρώματα. Ανάλογα με το ελαστικό, η διαδικασία μπορεί να πάρει από 15 λεπτά για ελαστικά επιβατικών αυτοκινήτων μαζικής παραγωγής μέχρι και σχεδόν 24 ώρες για ειδικά ελαστικά heavy-duty.
Το τελικό στάδιο αποτελείται από διάφορους ποιοτικούς ελέγχους, είτε με τη βοήθεια της τεχνολογίας (π..χ ακτίνες Χ για τυχόν κοιλότητες) είτε με το παλιό καλό γυμνό ανθρώπινο μάτι. Έτοιμο το λαστιχάκι σας κύριε.
Αέρας κοπανιστός? Άζωτο κοπανιστό!
Τα τελευταία χρόνια πολύς ντόρος γίνεται γύρω από τη χρήση καθαρού αζώτου για το φούσκωμα των ελαστικών, αντί για τον έτοιμο φυσικό αέρα που γεμίζει και τα πλεμόνια μας. Ακόμα και κάποια αυτοκίνητα παραγωγής (NissanGT-R) βγαίνουν από το εργοστάσιο με άζωτο στα ελαστικά τους, ενώ στα ελαστικά των αεροσκαφών χρησιμοποιείται ευρέως άζωτο εδώ και δεκαετίες. Κυκλοφορούν διάφορες θεωρίες γύρω από τα πλεονεκτήματα της χρήσης αζώτου έναντι του τυπικού αέρα, οι οποίες, ενώ έχουν κάποιο φυσικοχημικό υπόβαθρο για την τεκμηρίωση τους, εντούτοις στη πράξη οι διαφορές είναι αποδεδειγμένα από αμελητέες έως ανύπαρκτες. Μία προσέγγιση έχει να κάνει με το γεγονός ότι το άζωτο θεωρητικά δραπετεύει πιο δύσκολα από τους πόρους της γόμας και έτσι διατηρείται η επιθυμητή πίεση για μεγαλύτερο χρονικό διάστημα, λόγω μικρότερων απωλειών, ενώ η άλλη αφορά την απουσία υγρασίας, η οποία ως αναπόφευκτο κακό στον κανονικό αέρα, θα μας επηρεάζει τη πίεση των ελαστικών ανάλογα με την αύξηση της θερμοκρασίας τους περισσότερο από ότι το σκέτο άζωτο.
Αξίζει να μπλέξει κάποιος στην όλη διαδικασία σνομπαρίσματος του κοπανιστού αέρα που αναπνέουμε? Αν σκεφτείτε ότι ήδη ο αέρας ο «απλός» περιέχει σχεδόν 80% άζωτο και όλο το υπόλοιπο είναι πρακτικά οξυγόνο και πως ακόμα και με άζωτο να γεμίσετε, δεν θα φτάσετε ποτέ το 100% άζωτο σε σύσταση, η όλη ιστορία θα γίνει -αν γίνει- για διαφορά μικρού ποσοστού αύξησης της σύνθεσης του αερίου που βάζουμε σε άζωτο. Συμπερασματικά, οι αγωνιστικές ομάδες που κυνηγάνε το τελευταίο χιλιοστό του δευτερολέπτου, μπορεί στη πράξη να αξίζει να κάνουν το κόπο να ασχοληθούν με το θέμα του αζώτου, εσείς αν αισθάνεστε καλύτερα ψυχολογικά και μόνο, ιδού η Ρόδος ιδού και το πήδημα, η αυτοπεποίθηση στις στροφές είναι πιο σημαντική από κάθε χημική θεωρία!
Αέρια τέλος: Michelin Tweel
Και γιατί να μπλέκουμε γενικώς με πνευματικά ελαστικά και αέρια, ακόμα και αν μιλάμε για άζωτο, αφού έχουν τόσα μύρια προβλήματα? Κλαταρίσματα, θερμοκρασίες, πιέσεις, ας τα εξαφανίσουμε όλα. Έτσι σκέφτηκε η Michelin πριν χρόνια, παρουσιάζοντας το «Tweel», έναν πειραματικό τροχό που κάνει το φούσκωμα ανάμνηση του παρελθόντος. Εξωτερικά, υπάρχει ένα πέλμα ελαστικού με τις ιδιότητες και τη χάραξη που προσφέρει ένα συμβατικό ελαστικό, αλλά μετά από αυτό, αντί για αέρα συναντάμε μια διάταξη ακτινών πολυουρεθάνης με συγκεκριμένη ελαστικότητα που «προσομοιώνει» την αντίστοιχη δουλειά που θα έκανε ο αέρας. Οι ακτίνες ενώνονται με το πέλμα μέσω μίας ειδικής στεφάνης έδρασης, ενώ στο άλλο άκρο τους υπάρχει ένα υβρίδιο μουαγιέ και ζάντας (δείτε τις συνοδευτικές φωτογραφίες). Παίζοντας με την σκληρότητα των ακτινών μέσω του πάχους και της ακριβούς σύνθεσης του υλικού τους, δημιουργούνται και τα ανάλογα διαφορετικά χαρακτηριστικά συμπεριφοράς απόσβεσης και πρόσφυσης που επιθυμούμε και που σε ένα κανονικό ελαστικό θα καθορίζονταν από τις ιδιότητες συμπίεσης-αποσυμπίεσης του αέρα και της ευκαμψίας των πλαϊνών. Εξαλείφεται επίσης η ανάγκη για αισθητήρες πίεσης αέρα (TPMS), σύμφωνα με τη Michelin το πέλμα κρατάει πολύ περισσότερο από πλευράς φθοράς ενώ είναι και απλό στη κατασκευή του. Στα μειονεκτήματα του περιλαμβάνονται ο αυξημένος θόρυβος, η δημιουργία κραδασμών από κάποιες ταχύτητες και άνω, καθώς και οι μεγαλύτερες τριβές σε σχέση με τα συμβατικά ελαστικά. Μέχρι ώρας δεν πέρασε κάτι ανάλογο στη παραγωγή... Η Bridgestone παρουσίασε πολύ πρόσφατα την δική της εκδοχή του Airless ελαστικού, αντίστοιχης φιλοσοφίας, αλλά με λυμένα τα προβλήματα παραγωγής που συνάντησε η Michelin στο Tweel. Περισσότερα για το Airless της Bridgestone στο Tech Corner του παρόντος τεύχους. Πήξαμε στο λάστιχο αυτό το μήνα
Πολύ ψωμί...
...υπάρχει ακόμα στο θέμα «ελαστικά» και να είστε σίγουροι ότι έχουμε σκοπό, ως είθισται στις σειρές των Know How, να το φάμε μέχρι το τελευταίο του ψίχουλο. Αυτό το μήνα προσπαθήσαμε να επικεντρωθούμε κυρίως στη πλευρά του ελαστικού την οποία «βλέπει το μάτι», με άλλα λόγια τις πιο χειροπιαστές από τις ποικίλες ιδιότητες και χαρακτηριστικά του. Με αυτά για εφόδια, ετοιμαστείτε τον επόμενο μήνα για μπάνιο σε πιο βαθιά νερά (θα ‘χει ζεστάνει και ο καιρός επιτέλους): η πεμπτουσία των ιδιοτήτων ενός ελαστικού βρίσκεται σε αυτά που όχι μόνο δεν φαίνονται με το μάτι, αλλά που ούτε καν οι κλασικοί φυσικοί νόμοι και τύποι δεν μπορούν να εξηγήσουν και που ωστόσο ξέρουμε στη πράξη ότι ισχύουν παντού και πάντα. Μέχρι τότε ερωτευτείτε ελεύθερα, είναι το μόνο αντίδοτο στη κρίση, καρατσεκαρισμένο...
Αρθρογράφος
Δοκιμές Αυτοκινήτου CarTest.gr
Η νέα Alfa Romeo Tonale, λίγο πριν κάνει το επίσημο ντεμπούτο της στους δρόμους της Ευρώπης, βρέθηκε στο Grand Prix της Imola τιμώντας την Ιταλική κατ...